Refuelling Automation in Open-Pit Mines with Automated Dispatcher
- Mindshift Analytics
- Aug 3, 2024
- 2 min read
Updated: Aug 10, 2024
INTRODUCTION
Our Automated Fuel Dispatcher application optimizes diesel bowser movement in open-pit mines, ensuring that heavy machinery (HEMM) are refueled efficiently. This interactive app, installed on dashboard-mounted tablets, provides live fuel and geo-location data, empowering operators with comprehensive information on vehicle locations, criticality levels, and fuel status. With real-time information, the application guides operators to the best refueling sequence and route, mitigating the burden of manual fuel dispatch coordination, reducing dispatch errors and enhancing fleet up-time.
KEY BENEFITS
Eliminate production losses while HEMMs wait for refueling.
Reduce fuel bowser congestion with streamlined dispatches.
Redeploy dispatch staff engaged in manual dispatch coordination.
HOW IT WORKS
Previously, operators relied on walkie-talkies or cell phones to call for emergency fuel requirements. The manual dispatch coordinators followed a fixed daily itinerary and schedule that led to inefficiencies. With cell phones now banned for safety reasons, our app fills the gap by providing a digitized, automated solution.
Diesel bowser operators can now log into the Automated Fuel Dispatcher app running on dashboard mounted touch screen tablets. The app provides Bowser operators with an automated dispatch workflow. It efficiently prioritizes fuel dispatch to truck and machinery most in need of fuel (based on their live tank balances). Live geo-locations of trucks and machinery creates optimal dispatch routing, ensuring on-timely refueling. More field equipment stays productive as refueling wait times are reduced. The app also reduces fuel dispatcher workload.
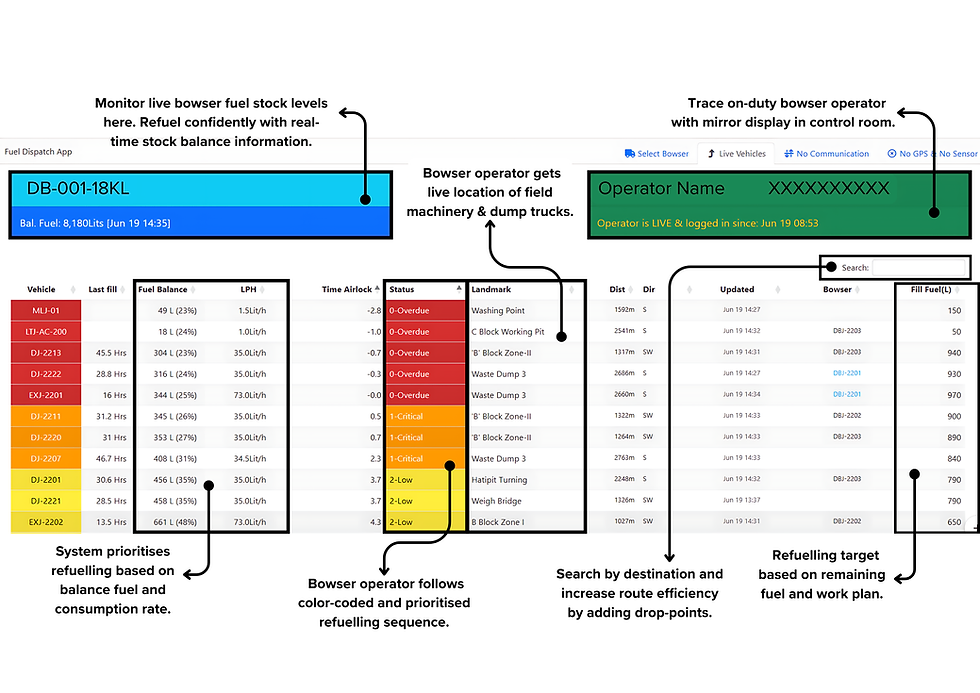
IMPACT

During refueling, mine operators report that HEMM (Heavy Earth Moving Machinery) operators often only refuel the bare minimum quantity needed to complete immediate tasks. While this saves time in the short run, it increases the frequency of small refuels. These refueling requests tend to bunch at the start of a shift, with about 5% of operators logging into machinery and trucks with nearly empty tanks. This crowding of refueling requests results in an average delay of about 20 minutes per affected HEMM. For a medium-sized mine with 150 fleet running 2 shifts, this delay translates into a productivity loss of over 1,800 hours annually, costing the mine approximately US$ 90,000 (₹75 Lacs).
Additionally, frequent smaller refuels increase bowser travel time and distance, severely loading service capacity. To add capacity, mine operators often hire diesel bowsers on contract, costing an average of US$ 15,000 (₹12 Lacs) annually per bowser.
Our Automatic Fuel Dispatcher App transforms this scenario by continuously monitoring machinery and truck fuel levels and geo-coordinates. It dynamically prioritizes and optimally routes the diesel bowser, ensuring vehicles are adequately fueled and ready to operate. This significantly reduces downtime and production losses, enhancing operational efficiency and resulting in substantial cost savings. The app streamlines dispatches, freeing up to 50% of bowser capacity for open-pit mines and eliminating the need for costly contract bowsers.
Experience seamless, cost-effective refueling that keeps your heavy machinery running smoothly and your bottom line healthy.
CONCLUSION
Our Automatic Fuel Dispatcher App significantly enhances operational efficiency and productivity while achieving substantial cost savings. By addressing key issues in refueling operations, the app ensures smooth, seamless, and cost-effective refueling that keeps your heavy machinery running optimally and your bottom line healthy. Each intervention brings savings in both time and money.
Comments